Discover everything about pressure measurement—its definition, working principles, and various types. Learn how pressure is measured, the fundamental concepts behind it, and the different sensors and devices used across industries for accurate and reliable results.
Pressure is a key concept in physics and fluid mechanics, representing the force applied per unit area on a surface. It is defined as the ratio of the force acting perpendicular to a surface to the area across which the force is distributed. Being a scalar quantity, pressure is commonly measured in units such as pascals (Pa), pounds per square inch (psi), or atmospheres (atm). In fluid mechanics, pressure plays a vital role in influencing fluid behavior, including flow dynamics, forces exerted by fluids on objects, and the transmission of forces within a fluid flow.
This blog will address all your queries related to pressure measurement, its underlying principles, and the different types of pressure-measuring devices.
Pressure Measurement
Pressure and its measurement are essential across numerous industries and applications, as it quantifies the force exerted by a fluid or gas on its surroundings. Accurate pressure monitoring is vital for maintaining safety, efficiency, and optimal system performance. Devices such as manometers, pressure transducers, and pressure gauges are commonly used to measure and regulate pressure, ensuring smooth and reliable operation of various processes and systems.
What is Pressure Messuremnt?
Pressure measurement refers to the process of determining the force exerted by a fluid (liquid or gas) on a surface per unit area. It is a fundamental concept in physics and engineering, essential for maintaining the safety, efficiency, and functionality of various systems and industrial processes. The standard formula for pressure is: Pressure =Force/Area
The unit of pressure in the International System of Units (SI) is the pascal (Pa), where one pascal equals one newton per square meter. Other common units include pounds per square inch (psi), bar, and atmospheres (atm).
Pressure measurement is critical in industries like oil and gas, automotive, aerospace, chemical processing, and water treatment. Accurate pressure readings help in monitoring system performance, preventing equipment failure, and ensuring operational safety.
There are several types of pressure, including absolute pressure, gauge pressure, differential pressure, and atmospheric pressure. Different instruments are used based on the type of pressure being measured. Common pressure-measuring devices include manometers, pressure gauges, and pressure transducers.
For example, in fluid mechanics, pressure measurement helps analyze fluid flow, calculate forces acting on surfaces, and manage fluid systems effectively. In medical applications, devices like blood pressure monitors are used to assess patient health.
Types of Pressure
Pressure can be classified into various types based on the reference point used for measurement. Understanding these different types is essential in fields like fluid mechanics, engineering, and industrial processes. Here are the main types of pressure:
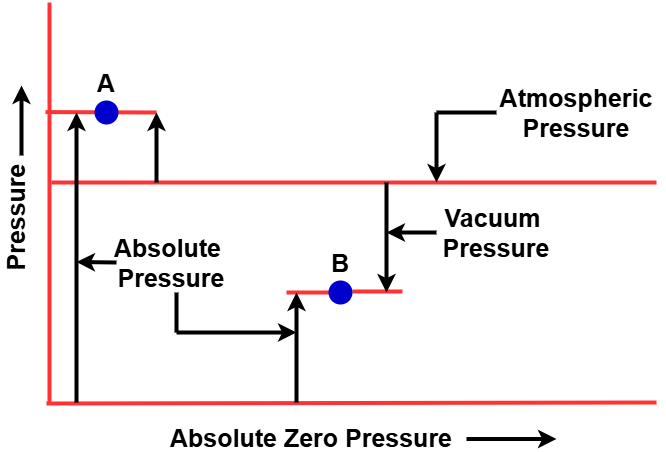
1. Atmospheric Pressure
Atmospheric pressure is the pressure exerted by the Earth’s atmosphere on everything at the surface. It is caused by the weight of the air above us and varies with altitude—decreasing as elevation increases. At sea level, the standard atmospheric pressure is approximately 101.325 kPa or 1 atm. Barometers are commonly used to measure atmospheric pressure, which plays a vital role in weather forecasting and aviation.
2. Absolute Pressure
Absolute pressure is measured relative to a perfect vacuum (zero pressure). It includes the atmospheric pressure and any additional pressure applied by a fluid or gas. The formula for absolute pressure is:
Absolute Pressure=Gauge Pressure+Atmospheric Pressure
Absolute pressure is crucial in scientific research, where precise measurements are needed, such as in vacuum systems and deep-sea applications.
3. Gauge Pressure
Gauge pressure measures the pressure relative to atmospheric pressure. When a pressure gauge reads zero, it means the measured pressure is equal to atmospheric pressure. Most industrial pressure gauges measure gauge pressure because they only reflect the pressure that exceeds atmospheric pressure. Common applications include tire pressure monitoring and pressure measurement in pipelines.
4. Differential Pressure
Differential pressure refers to the difference between two pressure readings within a system. It is commonly used in fluid flow measurement, filter monitoring, and level measurement. Devices like differential pressure gauges and transmitters are used to monitor this pressure, ensuring optimal system performance and detecting blockages or leaks.
5. Vacuum Pressure
Vacuum pressure measures pressures lower than the atmospheric pressure but not an absolute vacuum. It is often used in applications like vacuum packaging, semiconductor manufacturing, and vacuum pumps. Vacuum pressure can be expressed as either absolute or gauge pressure, depending on the reference point.
Units of Pressure
Pressure can be measured and expressed in various units depending on the measurement system and the application. Here are some of the most commonly used units:
- Pascal (Pa): The Pascal is the SI unit of pressure, defined as one newton per square meter (N/m²). Named after the French mathematician and physicist Blaise Pascal, it is widely used in scientific and engineering fields.
- Atmosphere (atm): This unit is commonly used in meteorology and general scientific contexts. One atmosphere is approximately equal to the average atmospheric pressure at sea level, which is around 101,325 pascals.
- Bar (bar): Equal to 100,000 pascals, the bar is frequently used in industrial and technical applications due to its convenient size for measuring higher pressures.
- Pounds per Square Inch (psi): Used primarily in engineering, automotive, and industrial applications, psi measures the pressure exerted by a pound-force over a square-inch area. One psi equals approximately 6,894.76 pascals.
- Torr: Named after Italian physicist Evangelista Torricelli, the inventor of the mercury barometer, one torr is equal to 1/760th of an atmosphere or approximately 133.322 pascals. It is mainly used in vacuum measurements.
- Millimeter of Mercury (mmHg): Commonly used in medical and scientific fields, especially for measuring blood pressure, one mmHg corresponds to the pressure exerted by a one-millimeter column of mercury and equals approximately 133.322 pascals.
These units are essential for accurately measuring and monitoring pressure across various scientific, industrial, and medical applications.
Pressure Measurement Methods
Pressure measurement involves determining the force exerted by a fluid or gas on a surface. Accurate pressure measurement is crucial across various applications, such as industrial processes, environmental monitoring, and engineering systems, ensuring safety, efficiency, and optimal performance.
Several common methods are used to measure pressure, including:
- Manometers: Devices that measure pressure by balancing a fluid column against the pressure being measured.
- Mechanical Pressure Gauges: Instruments that use mechanical elements, such as Bourdon tubes or diaphragms, to measure and display pressure.
In the following sections, we will discuss these pressure measurement methods in detail.
Manometer
Manometers are basic instruments used to measure pressure by balancing it against a liquid column, usually mercury or water. The height of the liquid column is directly proportional to the pressure applied. Manometers are generally classified into two types:
- Simple Manometer
- Differential Manometer
Types of Simple Manometer
Several types of simple manometers are commonly used for pressure measurement, each designed for specific applications and accuracy levels. The main types include:
Piezometer Manometer
A piezometer manometer is a simple device used to measure the pressure of liquids, particularly in open systems. It consists of a vertical transparent tube connected to a container holding the fluid. The liquid rises in the tube until the pressure is balanced by the weight of the liquid column.
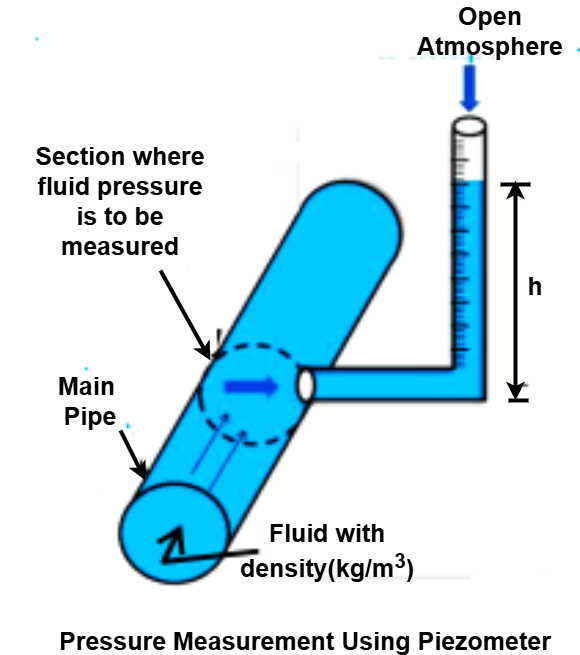
The height of this column directly indicates the pressure at that point. Piezometers are ideal for measuring low pressures but are unsuitable for gases or high-pressure applications. They are commonly used in hydraulic and soil mechanics studies.
Single-Column Manometer
A single-column manometer is a variation of the U-tube manometer, designed for measuring small pressure differences with greater sensitivity. It consists of a vertical column connected to a large reservoir, which minimizes liquid level changes in the reservoir when pressure is applied. The height of the liquid in the narrow column reflects the pressure being measured. These manometers are suitable for low-pressure measurements in gases and liquids and are commonly used in laboratories and industrial applications for precise pressure readings.
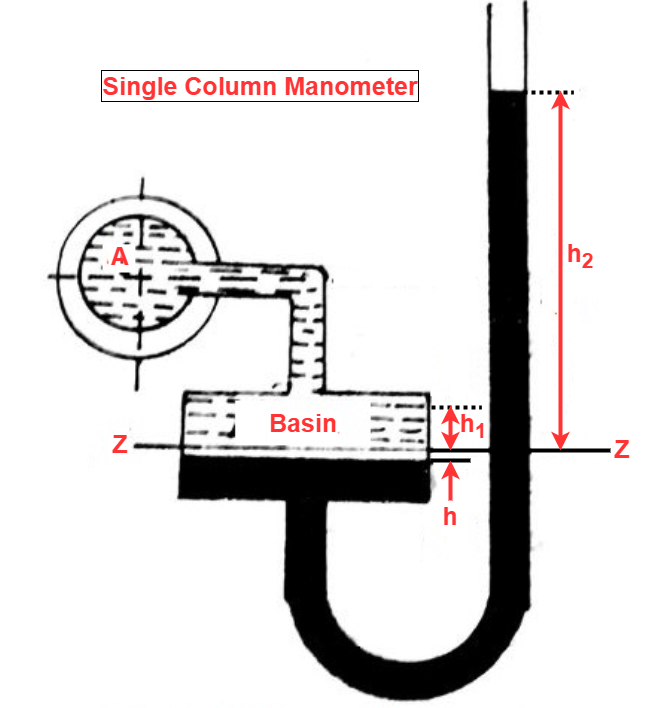
U-Tube Differential Manometer
A U-tube differential manometer is used to measure the pressure difference between two points in a system. It consists of a U-shaped tube filled with a liquid, typically water or mercury. The two ends of the tube are connected to different pressure points. The difference in liquid levels in both arms reflects the pressure difference between the two points. This type of manometer is commonly used in fluid mechanics, HVAC systems, and industrial applications to ensure accurate pressure monitoring and system balance.
Inverted U-Tube Differential Manometer
An inverted U-tube differential manometer is designed to measure small pressure differences, especially between two gas columns. It consists of an inverted U-shaped tube filled with a light liquid, such as oil. The two ends are connected to different pressure points, and the difference in liquid levels indicates the pressure difference. This type of manometer is ideal for measuring low-pressure variations and is commonly used in ventilation systems, gas flow measurements, and laboratory experiments requiring precise pressure readings.
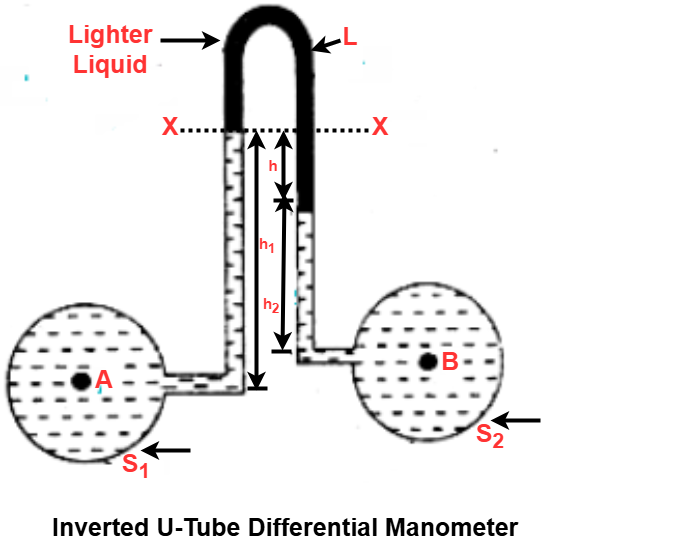
U-Tube Manometer
A U-tube manometer is a simple and reliable device used to measure pressure in liquids and gases. It consists of a transparent U-shaped tube partially filled with a liquid, typically mercury or water. One end is connected to the pressure source, while the other may be open to the atmosphere or another pressure point. The pressure is determined by the difference in liquid levels in both arms of the tube. U-tube manometers are widely used in laboratories, HVAC systems, and industrial applications for accurate pressure measurement.

Inclined Manometer
An inclined manometer is a precision instrument used to measure small pressure differences with high sensitivity. It features a transparent tube filled with liquid, positioned at an angle rather than vertically. This inclination increases the scale length for a given pressure change, allowing for more accurate readings of low pressures. Inclined manometers are commonly used in applications like airflow measurement in HVAC systems, laboratory experiments, and other settings where precise low-pressure measurements are essential. They are particularly effective for detecting minor pressure variations.
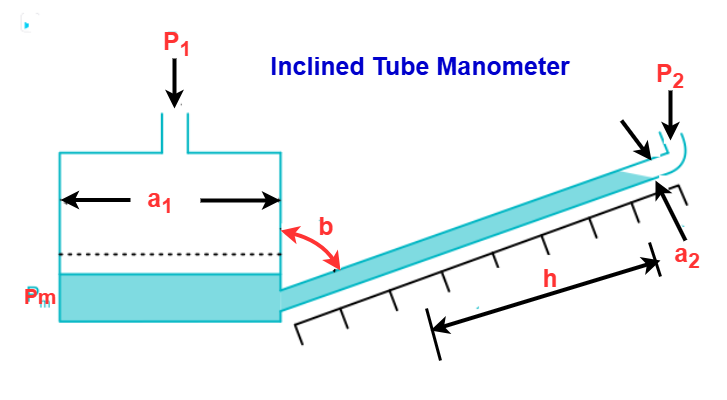
Well-Type Manometer
A well-type manometer is a variation of the U-tube manometer, designed for measuring small pressure differences with improved readability. It consists of a large reservoir (well) on one side and a narrow vertical tube on the other. When pressure is applied, the liquid level in the well changes slightly, while the movement in the narrow tube is more pronounced, making it easier to read. Well-type manometers are widely used in laboratories, HVAC systems, and industrial applications requiring precise low-pressure measurements.
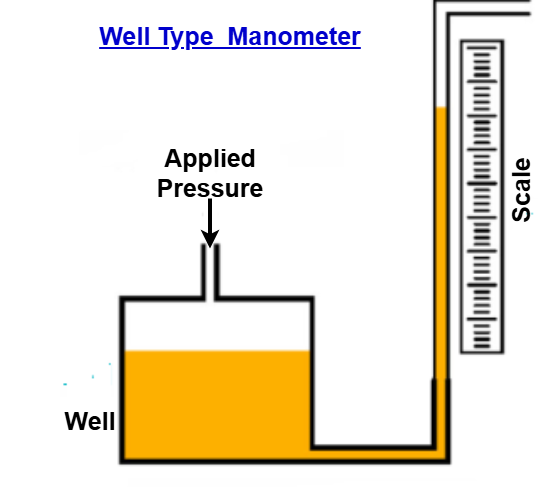
Mechanical Pressure Gauges
Mechanical gauges, including Bourdon and diaphragm pressure gauges, are commonly used for measuring pressure in boilers, pipelines, and other systems where tube gauges may not be practical. These gauges operate using elastic elements that deform when pressure is applied. The deflection of these elements is proportional to the pressure, allowing for accurate and reliable readings. Their durability and ease of use make them ideal for industrial, mechanical, and process control applications.
Bourdon Pressure Gauge
A Bourdon pressure gauge is a widely used mechanical device for measuring pressure in gases and liquids. It features a curved, hollow, elastic tube that straightens when exposed to pressure. The movement of the tube is transferred to a pointer through a mechanical linkage, displaying the pressure reading on a dial. Known for its accuracy, durability, and simplicity, the Bourdon gauge is commonly used in industrial applications, including boilers, hydraulic systems, and pipelines, to monitor and control pressure effectively.
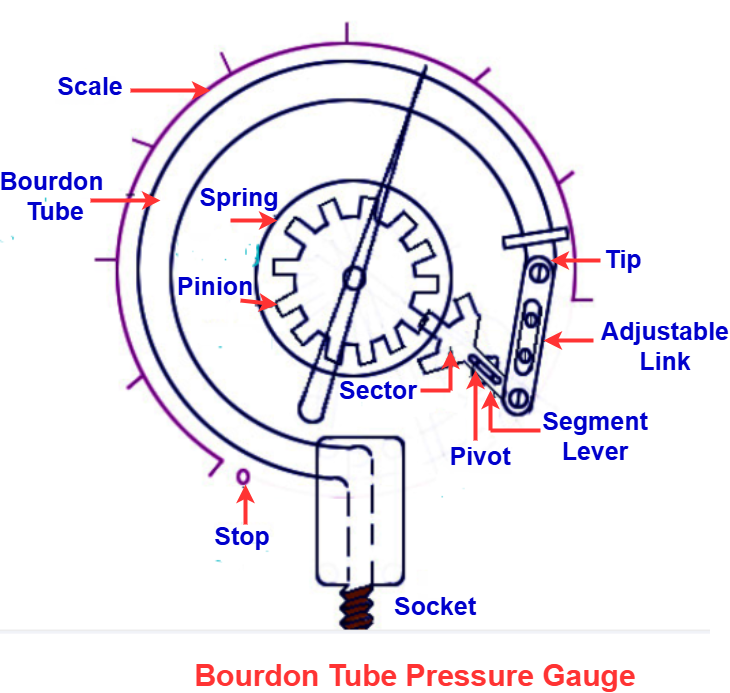
Diaphragm Gauge
A diaphragm gauge is a mechanical pressure-measuring device that uses a flexible diaphragm as the sensing element. When pressure is applied, the diaphragm deflects, and this movement is converted into a readable value through a mechanical linkage or electrical signal. Diaphragm gauges are ideal for measuring low to moderate pressures and are commonly used in industries dealing with corrosive fluids, gases, or sanitary applications. They provide accurate, stable readings and are widely used in chemical, pharmaceutical, and food processing industries.
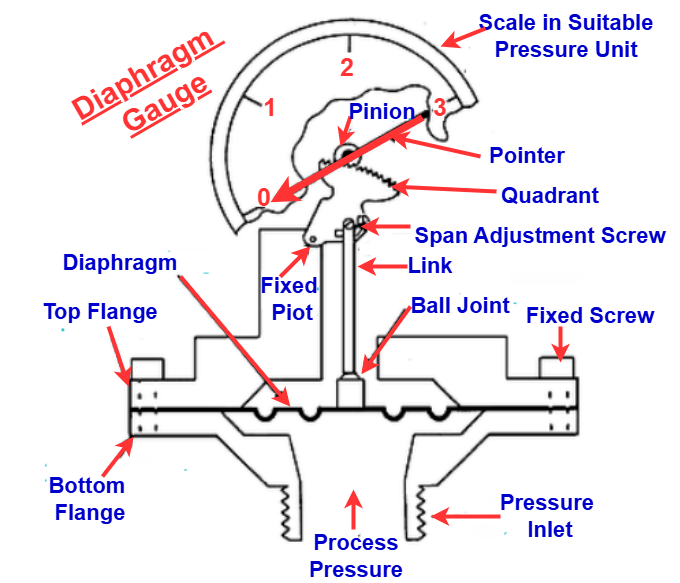
Differential Pressure Gauge
A differential pressure gauge measures the pressure difference between two points in a system. It typically features two input ports connected to separate pressure sources, and the gauge displays the difference between them. These gauges are essential for monitoring filters, flow rates, and level measurements in tanks. They are widely used in HVAC systems, industrial processes, and fluid dynamics applications to ensure optimal performance and detect blockages, pressure drops, or system imbalances. Their accuracy and reliability make them vital for efficient system monitoring.
Pressure Measurement Basic Principles
Pressure measurement relies on several fundamental principles to determine the force exerted by a fluid or gas. Key principles that form the basis of pressure measurement include:
Pascal’s Law: Pascal’s Law states that when pressure is applied to a confined fluid, it is transmitted equally in all directions throughout the fluid. This principle is fundamental in hydraulic systems, where applied pressure generates force uniformly, allowing for efficient operation of devices like hydraulic lifts and brakes.
Elasticity: Elasticity refers to a material’s ability to return to its original shape after being deformed by an applied force. In pressure measurement, elastic elements like Bourdon tubes, diaphragms, and bellows deform proportionally to the applied pressure. This deformation is then translated into readable pressure values.
Strain: Strain is the deformation experienced by a material when subjected to an external force or pressure, expressed as the change in length relative to the original length. In pressure measurement, strain gauges detect these deformations, converting mechanical strain into electrical signals for accurate pressure readings in various industrial applications.
Fluid Column Height: Fluid column height is a principle used in pressure measurement where the height of a liquid column corresponds to the pressure exerted by the fluid. Devices like manometers utilize this concept, with the pressure being directly proportional to the liquid’s height, density, and acceleration due to gravity.
Piezoelectric Effect: The piezoelectric effect occurs when certain materials generate an electric charge in response to applied mechanical stress. In pressure measurement, piezoelectric sensors convert pressure-induced deformation into electrical signals. These sensors are widely used in applications requiring rapid response and high sensitivity, such as in the aerospace and automotive industries.
Capacitance: Capacitance in pressure measurement involves changes in the distance between two conductive plates due to applied pressure. As the pressure deforms a diaphragm, the gap between the plates changes, altering the capacitance. This change is measured and converted into a pressure reading, offering high sensitivity and accuracy.
Type of Pressure Distribution
In fluid mechanics, pressure distribution describes how pressure changes within a fluid or gas flow. The distribution pattern is influenced by flow characteristics and the forces acting on the fluid. Here are three common types of pressure distribution:
Uniform Pressure Distribution:: When pressure remains constant across a fluid or surface, it is known as uniform pressure distribution. This typically occurs in static fluids or when external forces are evenly applied. It ensures consistent force distribution, making it essential for applications like hydraulic systems, where equal pressure is crucial for efficient operation.
Linear Pressure Distribution: When pressure changes at a constant rate across a fluid or surface, it is known as linear pressure distribution. This typically occurs in static fluids under gravity, such as water in a tank, where pressure increases proportionally with depth. It is essential for analyzing fluid statics and hydrostatic forces.
Non-linear Pressure Distribution:: When pressure changes unevenly across a fluid or surface, it is referred to as non-linear pressure distribution. This typically occurs in dynamic fluid systems, such as around airfoils or in turbulent flow. Factors like velocity changes, fluid acceleration, and external forces contribute to the non-linear variation in pressure.
Sensors Used for Pressure Measurement
Various types of sensors are used for pressure measurement, each operating on different principles and suited for specific applications. Here are some commonly used pressure sensors:
Capacitive Pressure Sensor: A capacitive pressure sensor measures pressure by detecting changes in capacitance between two conductive plates separated by a dielectric material. When pressure is applied, the diaphragm deforms, altering the distance between the plates and changing the capacitance. These sensors offer high sensitivity and are used in industrial and medical applications.
Piezoelectric Pressure Sensor: A piezoelectric pressure sensor operates by generating an electrical charge in response to mechanical stress on piezoelectric materials. When pressure is applied, the material deforms, producing a voltage proportional to the pressure. These sensors are ideal for dynamic pressure measurements in automotive, aerospace, and industrial applications.
Optical Pressure Sensor: An optical pressure sensor measures pressure by detecting changes in light properties, such as intensity, phase, or wavelength, within an optical fiber. Pressure-induced deformation alters these light signals. These sensors offer high accuracy and immunity to electromagnetic interference, making them ideal for medical, aerospace, and industrial applications.
Resonant Wire Pressure Sensor: A resonant wire pressure sensor measures pressure by detecting changes in the natural frequency of a tensioned wire. When pressure is applied, the tension on the wire changes, altering its resonant frequency. These sensors offer high precision and stability, making them ideal for aerospace, industrial, and scientific applications.
Strain Gauge Pressure Sensor: A strain gauge pressure sensor measures pressure by detecting the deformation of a material under applied force. The strain gauge, bonded to a diaphragm, changes its electrical resistance when pressure causes deformation. These sensors are widely used in industrial, automotive, and aerospace applications for their accuracy and reliability.
Differential Pressure Sensor: A differential pressure sensor measures the difference in pressure between two points. It typically uses diaphragms, strain gauges, or capacitive elements to detect pressure variations. These sensors are essential in applications like flow measurement, filter monitoring, and HVAC systems, ensuring accurate and efficient system performance.
Read Next: