Instrumentation and Controls form the backbone of every modern industrial system, ensuring processes run efficiently, safely, and reliably. Whether it’s a chemical plant, a power station, or a water treatment facility, instrumentation and controls play a pivotal role in monitoring and manipulating variables such as pressure, flow, temperature, and level.
In this guide, we’ll explore what is instrumentation, its role in automation, the different types of instrumentation, and how instrumentation control engineering shapes industrial processes.
What is Instrumentation?
According to the International Society of Automation (ISA), instrumentation is the collective term for instruments and their use for the purpose of measurement, observation, and control of process variables.
Simply put, instrumentation involves tools and devices that measure physical quantities like:
- Pressure
- Temperature
- Flow
- Level
- Density
- Viscosity
- Radiation
These measurements are critical for real-time monitoring and management of industrial systems.
In modern industries, Instrumentation and Controls form the backbone of automated operations. From oil refineries to power plants, these instruments help ensure safety, efficiency, and accuracy. For instance, if the pressure inside a reactor exceeds the safe limit, pressure transmitters alert the system, and control valves act automatically to regulate the situation—often without human intervention.
This is where instrument control engineering plays a key role. Engineers in this field design, develop, and maintain the systems that gather data from sensors and transmitters, and then process this information through programmable controllers like PLCs (Programmable Logic Controllers) or DCS (Distributed Control Systems).
Instrumentation is not just about measurement; it’s also about control. With precise data, systems can make real-time decisions—such as adjusting temperature, controlling flow rates, or shutting down equipment during anomalies. This seamless integration of measurement and control makes instrumentation control engineering essential in any process-driven industry.
Moreover, the reliability and accuracy of these instruments directly affect product quality, plant safety, and energy efficiency. Therefore, every instrumentation and control engineer plays a pivotal role in optimizing system performance and achieving operational excellence.
What is Instrument Control Engineering?
Instrument control engineering—also known as instrumentation control engineering—is a specialized branch of engineering that focuses on the design, configuration, integration, and maintenance of instruments and control systems in automated environments.
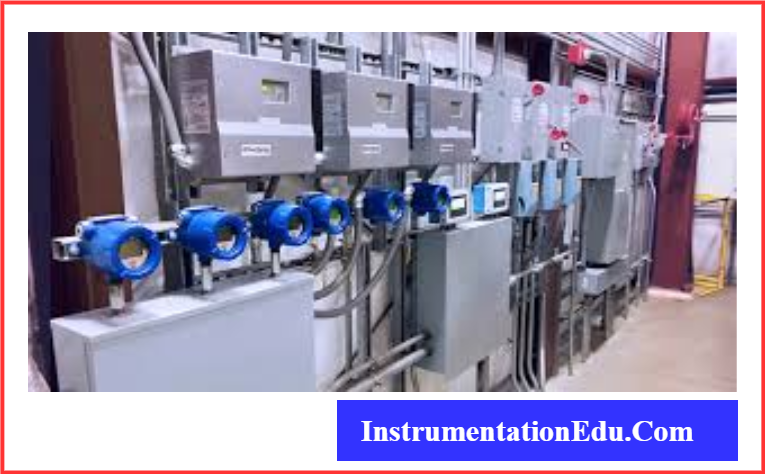
Professionals in this field work extensively with:
- Sensors and transmitters
- Control valves
- PLCs (Programmable Logic Controllers)
- DCS (Distributed Control Systems)
- SCADA (Supervisory Control and Data Acquisition)
The objective of instrumentation control engineering is to ensure that systems operate within precise and safe parameters, ultimately optimizing performance, reliability, safety, and energy efficiency.
An instrumentation and control engineer is responsible for selecting the appropriate instruments, calibrating them, and integrating them into larger control systems that monitor real-time data. These engineers also develop algorithms and control strategies to automate responses to changing conditions—making the entire industrial process more intelligent and less dependent on manual intervention.
In industries such as oil and gas, pharmaceuticals, manufacturing, and power generation, instrumentation and controls are critical. Properly functioning control systems help prevent equipment failures, reduce downtime, improve product quality, and enhance workplace safety.
As automation continues to evolve, instrument control engineering is becoming more important than ever. Engineers must stay updated with new technologies, such as IoT-enabled smart sensors, AI-powered analytics, and cloud-based SCADA systems, to design advanced control architectures that are robust, scalable, and future-ready.
Instrumentation and Controls in Action
Instrumentation and controls are at the heart of modern industrial automation. They form the backbone of control loops, where real-time data from sensors is used to make precise adjustments to maintain optimal process conditions—without human intervention. These systems enhance efficiency, safety, and accuracy in a wide range of industries, including oil and gas, manufacturing, water treatment, and energy production.
Key Components of a Control Loop:
Component | Function |
---|---|
Sensors | Detect process variables (e.g., temperature, pressure) |
Transmitters | Convert physical readings into standardized signals |
Controllers | Evaluate input data and decide corrective actions |
Final Elements | Actuators or valves that execute the control action |
For instance, in a chemical processing plant, a temperature sensor detects a rise above the set point. The transmitter sends a 4–20 mA signal to a PLC (Programmable Logic Controller). Based on its programming, the controller instructs a control valve to open a cooling line, lowering the temperature back to the desired range.
This seamless coordination between sensing, communication, decision-making, and action is what defines an effective instrumentation and control system. Instrumentation control engineering ensures that each element performs reliably and accurately, keeping industrial processes stable, safe, and optimized.
Types of Instrumentation
Instrumentation can be broadly categorized based on the process variables they measure and the roles they perform within instrumentation and control systems. This classification is essential for selecting the right tool for a specific application in industries like power plants, petrochemicals, water treatment, and manufacturing.
Measurement Instruments:
These devices are used to quantify physical parameters, providing critical input to the control system:
- Pressure gauges and transmitters – Measure static and differential pressure.
- Temperature thermocouples and RTDs – Monitor heat in processes with high accuracy.
- Flow meters – Available in ultrasonic, magnetic, orifice plate, and turbine types for precise flow rate monitoring.
- Level sensors – Include radar, ultrasonic, and float-based sensors for measuring liquid levels in tanks or silos.
Control Instruments:
These devices interact with the process to bring variables back to their desired set points:
- Solenoid valves – Provide fast on/off control of fluids.
- Motorized control valves – Regulate flow or pressure in a process line.
- Circuit breakers and relays – Ensure safety and automatic switching.
- PID controllers – Perform real-time adjustments using proportional-integral-derivative logic.
Understanding the types of instrumentation is key for instrument control engineering, allowing engineers to design effective, reliable, and energy-efficient instrumentation control systems tailored to specific industrial demands.
Role of an Instrumentation and Control Engineer
An Instrumentation and Control (I&C) Engineer plays a vital role in the heart of industrial automation. These professionals are responsible for designing, developing, installing, and maintaining the instrumentation and control systems that monitor and regulate industrial processes. Their work ensures optimal performance, safety, and energy efficiency across sectors such as oil & gas, power generation, pharmaceuticals, and food processing.
Key responsibilities include:
- Designing control systems that meet specific process requirements.
- Selecting appropriate sensors and actuators for accurate data collection and system response.
- Calibrating, configuring, and testing instruments to ensure they deliver accurate measurements and reliable outputs.
- Troubleshooting faults in automation systems to minimize downtime.
- Implementing safety systems like alarms, interlocks, and emergency shutdowns to protect equipment and personnel.
- Integrating cutting-edge technologies such as IoT sensors, AI-based control algorithms, and digital twins for smarter automation.
I&C engineers serve as the eyes, ears, and analytical mind of any automated facility. They translate raw sensor data into actionable control strategies, ensuring machines and systems work harmoniously. Their expertise bridges the gap between field instrumentation and centralized control systems, enabling continuous, safe, and cost-effective industrial operations.
Importance of Instrumentation in Safety and Compliances.
Instrumentation is not merely about monitoring performance—it plays a crucial role in ensuring safety, regulatory compliance, and environmental protection. In industries such as chemical processing, oil and gas, pharmaceuticals, and nuclear power, precise measurement and control can mean the difference between smooth operation and catastrophic failure.
Inaccurate or faulty instrumentation can result in:
- Equipment failure due to unchecked pressure, temperature, or flow.
- Unplanned downtime, affecting productivity and profitability.
- Safety risks such as fires, explosions, or toxic exposure.
- Environmental hazards, including leaks or emissions violations.
- Legal penalties, regulatory shutdowns, and damage to the organization’s reputation.
Modern instrumentation systems are designed with built-in safety features like alarms, trip signals, and emergency shutdown mechanisms (ESD). These systems continuously monitor critical variables and initiate corrective actions automatically when parameters exceed safe limits.
Moreover, compliance with international standards such as IEC 61508 (functional safety), ISO 9001 (quality management), and OSHA guidelines is heavily dependent on robust instrumentation. Regular calibration, validation, and documentation of instrumentation are essential practices to meet these standards.
Ultimately, reliable instrumentation safeguards not just the machinery—but the people, the environment, and the long-term viability of industrial operations.
The Future of Instrumentation and Controls
With the rise of Industry 4.0, the landscape of instrumentation and control engineering is undergoing a profound transformation. Traditional analog systems are giving way to intelligent, connected, and data-driven technologies that are revolutionizing how industrial processes are monitored and controlled.
Smart sensors and transmitters now come with self-diagnostic capabilities, enabling predictive maintenance and reducing unexpected downtime. IoT-enabled controllers and wireless networks make real-time data collection more accessible, even in remote or hazardous environments. These advancements help streamline operations and increase efficiency.
Engineers today must be adept in emerging technologies, such as:
- Digital communication protocols (e.g., HART, Modbus, Foundation Fieldbus) that allow multi-variable transmission and device interoperability.
- Edge computing, which processes data locally at the device level, reducing latency and enhancing decision-making speed.
- Cloud integration, which enables scalable storage, advanced analytics, and remote monitoring capabilities.
- Cybersecurity frameworks to safeguard critical infrastructure from digital threats and vulnerabilities.
As systems become more autonomous and data-driven, the role of instrumentation and control engineers is evolving from system maintainers to strategic enablers of intelligent automation. Their ability to blend core engineering with digital innovation is essential for building the smart factories of the future.
Careers in Instrumentation
The field of instrumentation and control offers a wide range of rewarding career paths across many sectors, including oil & gas, power generation, water treatment, manufacturing, aerospace, pharmaceuticals, and even renewable energy. These roles are crucial for optimizing production, maintaining safety, and ensuring compliance in highly automated and regulated environments.
Some common job titles in this domain include:
- Instrumentation Engineer – Designs and implements control systems for industrial processes.
- Control Systems Engineer – Focuses on programming and maintaining automation hardware like PLCs, DCS, and SCADA.
- Instrument Technician – Handles the calibration, maintenance, and repair of field instruments.
- Instrumentation Technologist – Works on the integration of instrumentation into broader control systems and may assist with data acquisition and signal processing.
In addition to technical proficiency, professionals must also be skilled in documentation, system diagnostics, and process optimization. As industries adopt smart technologies, careers in this field increasingly require knowledge of network protocols, cybersecurity, and data analytics.
With automation continuing to grow, skilled instrumentation professionals are in high demand globally. This makes it a promising career
Conclusion: The Core of Automation
Instrumentation and controls are the heart of modern automation. From measuring a tank’s level to adjusting a turbine’s speed, these systems ensure everything runs smoothly, safely, and smartly.
Whether you’re just learning what is instrumentation, exploring instrumentation control engineering, or training to be an instrumentation and control engineer, the journey promises continuous learning, innovation, and impact.
Stay Tuned, Stay In Control
Let’s build smarter, safer, and more efficient systems—because in the world of industry, control is everything.
Read Next: