Discover the key differences between continuous and point level sensors, including how they work, their applications, and which is best for your needs. This article explores their distinct advantages and suitable industrial uses.
In the world of industrial automation and process control, accurate measurement of material levels within tanks, silos, or containers is critical. Level sensors are instrumental in providing this data, and they come in two primary types: continuous level sensors and point level sensors. Each type has its own applications, advantages, and mechanisms, making them suitable for different operational requirements. This article delves into the distinctions between these two types of level sensors, helping you understand which might be best suited for specific industrial applications.
Continuous Level Sensors
Continuous level sensors provide real-time level measurement by continuously monitoring the level of a material within a container. They offer a detailed measurement across the entire range of the container, providing output as an exact measurement which can be in the form of a percentage, distance, or volume.
How They Work: Continuous level sensors typically operate using technologies such as ultrasonic, radar, or laser. For instance, an ultrasonic level sensor emits sound waves towards the material surface, measuring the time it takes for the echo to return. This time is then converted into a level measurement. Similarly, radar level sensors use radio waves, while laser sensors use light pulses.
Applications: These sensors are crucial in industries where precise measurements are necessary to ensure optimal operation, such as in chemical processing, oil and gas, water management, and pharmaceuticals. They are ideal for processes that require exact control of material volumes during input or output, ensuring efficiency and safety.
Point Level Sensors
Point level sensors, on the other hand, are designed to alert when the material reaches a specific point in the container. They do not measure the material level continuously but rather act as indicators to signal high, low, or intermediate levels.
How They Work: Point level sensors typically function using capacitive, conductive, or float mechanisms. For example, a float-type point level sensor activates when the float rises or falls to a particular level. Conductive level sensors use the conductivity of the liquid to complete a circuit when the liquid reaches a set point.
Applications: Point level sensors are widely used in applications where it is only necessary to know if a container is full, empty, or if a certain critical level is reached. They are simpler and often less costly than continuous sensors, making them suitable for basic dewatering operations, overflow protection, and pump control.
Key Differences between Continuous and Point Level Sensors
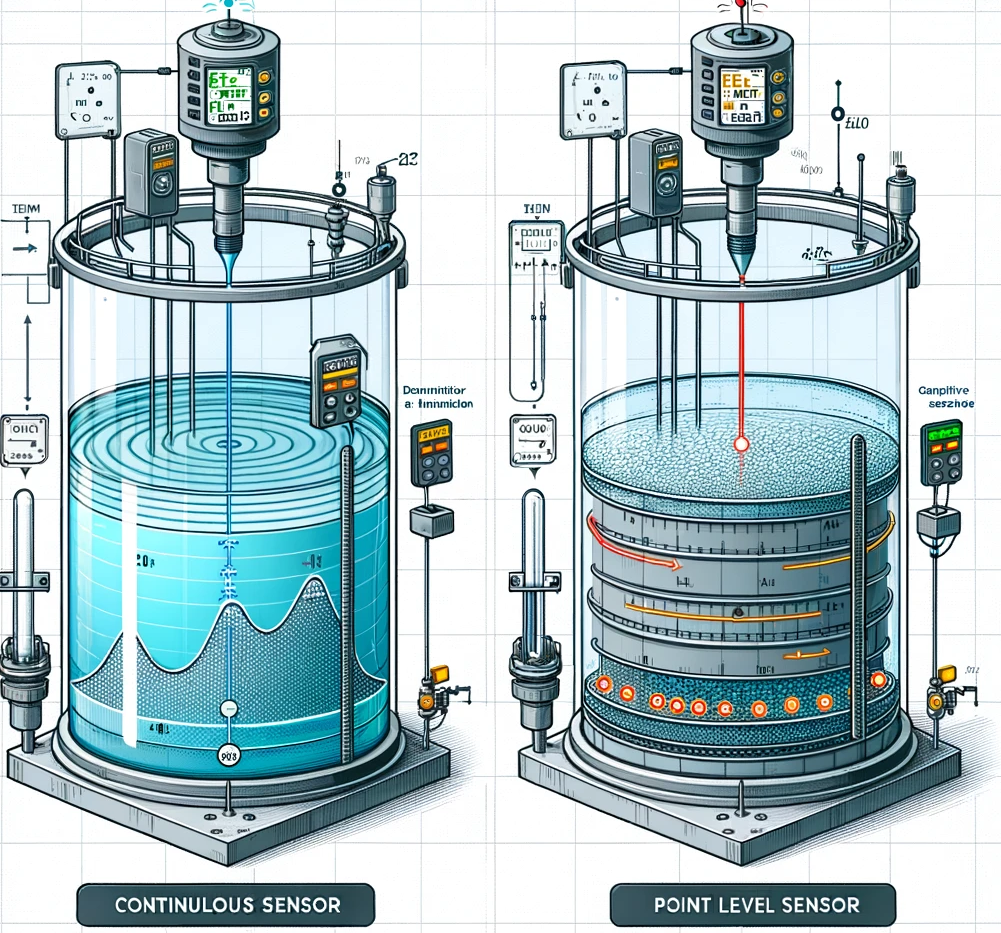
- Measurement Capability: Continuous sensors provide detailed and exact measurements across the entire range of a container. In contrast, point level sensors only provide confirmation when a specific level is reached.
- Cost and Complexity: Continuous level sensors are generally more complex and costly due to their detailed measurement capabilities and advanced technologies used. Point level sensors are simpler and more cost-effective, suitable for less critical applications.
- Application Suitability: Continuous level sensors are essential where constant monitoring and precise measurements are critical, whereas point level sensors are adequate for applications requiring basic level monitoring and overflow protection.
Conclusion
Choosing between continuous and point level sensors depends largely on the specific needs of the application. For environments requiring detailed and continuous monitoring of material levels, continuous level sensors are indispensable. For simpler tasks that only require basic monitoring or level alerts, point level sensors offer a practical and economical solution. Understanding these differences helps in selecting the right sensor technology that not only meets operational demands but also optimizes performance and safety.
Read Next: