A float switch is a versatile and essential device used in various industries for monitoring and controlling liquid levels in tanks and containers. This article explores the construction and working of float switches and their diverse applications.
What is a Float Switch?
A float switch is a device used to detect and control the level of liquid within a tank or container. It operates based on the principle of buoyancy, where a float, typically made of a lightweight and waterproof material, rises and falls with the liquid level. Switches are available in different sizes, ranging from small to large. There are two main styles of float switches: magnetic (also known as electromagnetic) and mechanical float type. The float switch symbol is displayed below.
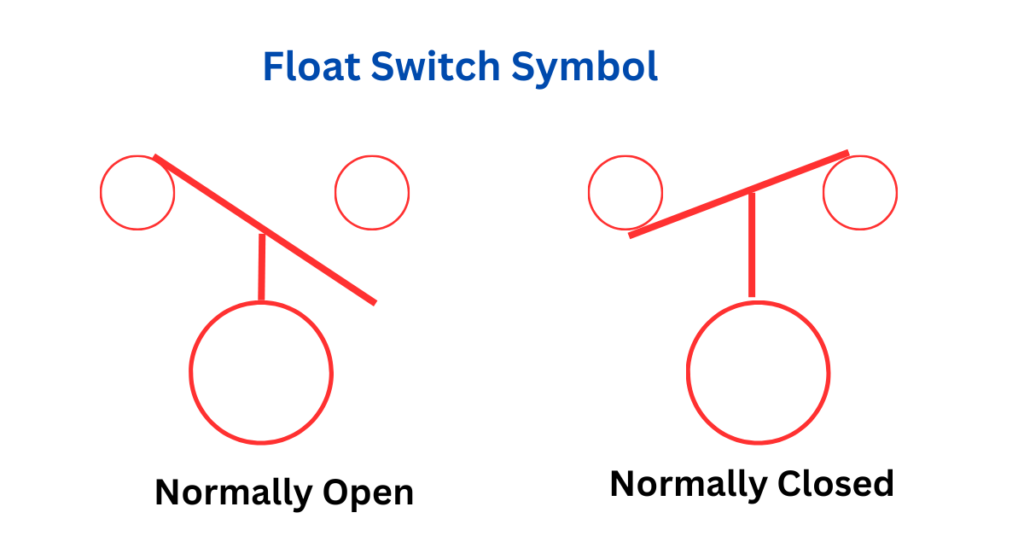
Construction of a Float Switch
A float switch is a simple yet effective liquid level sensor that includes a few key components:
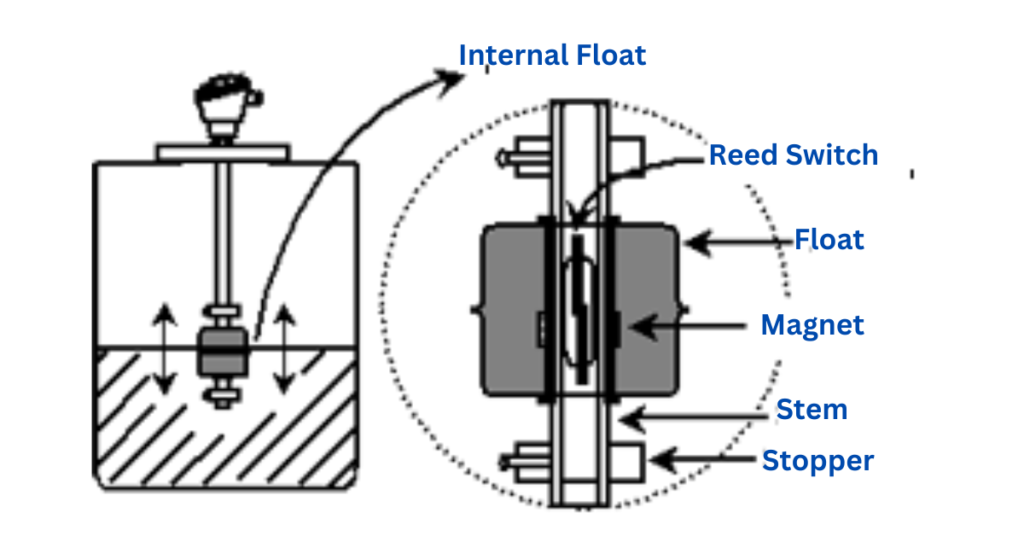
- Float: The most critical component, the float is usually a hollow or foam-filled ball that is buoyant and moves up and down with the liquid level.
- Stem: This is a rod that connects the float to the switch mechanism and guides the float’s movement.
- Switch Mechanism: Located either inside the float or at one end of the stem, this mechanism activates or deactivates electrical contacts based on the float’s position.
- Housing: All mechanical and electrical components are enclosed within a durable housing to protect against environmental factors and ensure reliable operation.
- Permanent Magnet: A switch contains a permanent magnet that moves up and down with the level of fluid in a guide tube. A reed contact is connected within the guide tube, and it is activated by the magnet as it approaches. The float magnet is non-magnetic and is surrounded by walls which are also non-magnetic.
The materials used for constructing float switches must be compatible with the liquids they monitor to avoid corrosion and ensure longevity. Common materials include plastics, stainless steel, and other metals.
Working of a Float Switch
The operation of a float switch is based on the buoyancy principle, which states that an object will float if the gravitational (downward) force is less than the buoyant (upward) force exerted by the fluid. Here’s how it works:
- As the liquid level in a tank rises, the float rises.
- Once the float reaches a predetermined high point, it triggers the switch to turn on (or off) an electrical circuit.
- Similarly, when the liquid level falls, the float descends and can switch the circuit back, indicating a low level.
This simple mechanism makes the float switch highly reliable and easy to use for basic control tasks such as filling or emptying a container.
Working of Electromagnet Float Switch
The operation of an electromagnet float switch is given below.
- Initial Position: When the liquid level is below the set point, the float rests in a lower position, keeping the switch circuit open (or closed, depending on the design).
- Rising Liquid Level: As the liquid level rises, the float also moves upward. This movement is transferred via the arm to the switch mechanism. In a standard float switch, this would directly trigger the switch contacts.
- Electromagnet Activation: In an electromagnet float switch, as the float reaches a certain height, it activates the electromagnet. The magnetism can be used to pull the contacts together or hold them apart more reliably than a mechanical action alone. This reduces wear on the contacts and provides more precise control.
- Stable Operation: The electromagnet helps maintain the position of the contacts until the liquid level changes sufficiently to de-energize the magnet. This can be particularly useful in applications where there is a lot of turbulence or where precise control over the switching action is needed.
- Return to Initial: As the liquid level falls, the float descends, reversing the process and either breaking or making the circuit again, depending on the configuration.
Working of Mechanical Float Switch
The operation of a mechanical float switch is straightforward:
- Initial State: In the resting state, the float is at a certain level due to the existing liquid level. Depending on the setup, this can either keep the electrical contacts closed or open.
- Rising Liquid Level: As the liquid level in the tank rises, the float rises along with it due to its buoyancy. The upward movement of the float lifts the connected stem or rod.
- Switch Activation: The movement of the stem operates the switch mechanism. In many designs, the stem is directly connected to a lever or arm inside the switch mechanism that controls the electrical contacts. As the lever moves, it changes the state of the contacts (from open to closed or vice versa).
- Circuit Completion or Interruption: Closing the contacts will complete an electrical circuit, often used to activate a device such as a pump, an alarm, or another type of indicator. Opening the contacts will break the circuit, which can be used to stop a pump or deactivate a system.
- Falling Liquid Level: Conversely, when the liquid level falls, the float descends, reversing the movement of the stem and the connected switch mechanism. This action typically returns the switch to its original state, reopening or reclosing the electrical contacts as needed.
Types of Float Switches
Float switches come in various types, each designed to cater to specific environmental and operational requirements. Understanding these different types can help in selecting the right float switch for a particular application. Here are some of the common types of float switches:
1. Vertical Float Switch
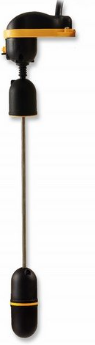
These switches are designed to move up and down along a vertical shaft, making them well-suited for narrow spaces. They are commonly used in small tanks and sump pump applications. When the liquid level changes, the vertical float rises or falls, triggering the switch mechanism at certain points. This type is simple and highly reliable for direct pump control.
2. Horizontal Float Switch
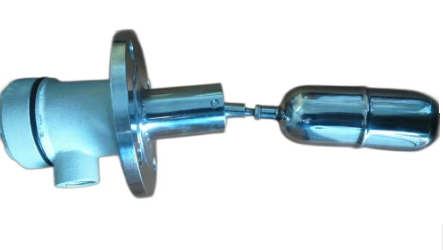
Horizontal float switches mount through the side of a tank and can move a float arm horizontally. As the liquid level reaches the float, it moves the arm, which activates the switch. These are ideal for applications where vertical space is limited, and they can be used to control multiple points by using more than one float on a single arm.
3. Cable Float Switch
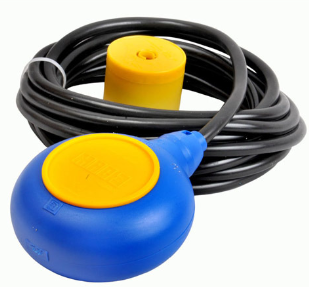
Cable float switches feature a float attached to a length of cable and can be used in wider or open spaces, such as large industrial tanks. The float moves up and down with the liquid surface, tilting at a certain angle to activate the switch. This type is versatile and can handle various liquids, including those with high viscosity or particulate content.
4. Electronic Float Switch
These switches use electronic sensors instead of mechanical floats. They are more precise and can be used in environments where mechanical parts might fail due to corrosion or sediment build-up. Electronic float switches use technologies like capacitance, ultrasonics, or optical sensors to detect liquid levels without direct contact.
5. Multi-level Float Switch
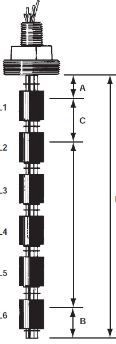
Multi-level float switches can monitor multiple liquid levels within a single device. They use several floats fixed at various heights on a central shaft to provide separate signals for different levels. This type is suitable for complex processes that require monitoring at various depths, such as chemical mixing or batch processes.
6. Mercury Float Switch
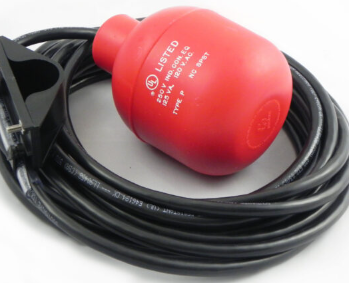
These contain mercury within the float that completes an electrical circuit when tilted. Mercury switches are very accurate but are less commonly used today due to environmental concerns related to mercury handling and disposal.
Applications of Float Switches
Float switches are used in a wide array of applications due to their simplicity and effectiveness. Some common uses include:
- Pump Control: In residential and commercial buildings for controlling water pumps in sump pits, preventing basement flooding.
- Tank Level Monitoring: In industrial settings, float switches are used to monitor fluid levels in chemical, food processing, and pharmaceutical industries.
- Alarms: They can activate alarms in systems requiring constant liquid level monitoring, such as in sewage treatment plants or oil tanks.
- HVAC Systems: Used to detect the level of collecting water in air-conditioning systems to prevent overflow or leakage.
- Automotive and Marine Applications: Float switches are used to monitor and control fuel or oil levels in tanks.
Advantages and Limitations
Advantages:
- Simplicity and ease of use
- Cost-effective
- Reliable and low maintenance
Limitations:
- Not suitable for viscous liquids or liquids with high particulate content as these can impede the float’s movement.
- Limited to point level detection rather than continuous measurement.
Conclusion
Float switches are fundamental components in systems that require reliable and cost-effective liquid-level control. Whether used in home sump pumps or large industrial tanks, the float switch remains a favored choice due to its straightforward design and dependable performance. Understanding how they work and where they can be effectively employed can help in selecting the right level control solution for any application.
Read Next: