Pressure gauge calibration is the process of ensuring the accuracy of a pressure gauge by comparing its readings to a known standard. This is achieved by either applying a known pressure and measuring the gauge’s response or comparing its output to a reference gauge. Calibration is essential for both analog and digital pressure gauges to maintain precise and reliable measurements. The process typically involves making necessary adjustments to align the gauge with industry standards and regulatory requirements.
How to Calibrate a Pressure Gauge
Calibrating a pressure measurement gauge ensures its accuracy and reliability by comparing its readings to a known standard. This process is essential for maintaining measurement precision in industrial, laboratory, and commercial applications. Various calibration equipment can be used, including a deadweight tester, pneumatic calibrator, or a hand pump calibrator. Regardless of the tool used, the general calibration steps remain consistent for both mechanical and digital pressure gauges.
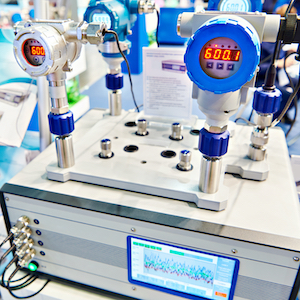
Below is a detailed step-by-step guide for calibrating a pressure gauge using a hand pump calibrator:
Step 1: Prepare for Calibration
- Ensure the calibration area is clean and free of environmental factors that could affect readings (e.g., temperature fluctuations, vibrations).
- Verify that the hand pump calibrator and the pressure gauge are in good working condition.
- Gather the necessary fittings, adapters, and reference instruments to ensure proper connections.
Step 2: Connect the Pressure Gauge
- Attach the hand pump calibrator to the pressure gauge using the appropriate adapter or fitting.
- Ensure the connection is secure and leak-free to prevent inaccurate readings.
Step 3: Set the Desired Pressure
- Use the hand pump calibrator to set a specific known pressure value within the gauge’s operating range.
- Start with a lower pressure value and gradually increase it to cover multiple test points.
Step 4: Apply and Observe Pressure
- Slowly pump the calibrator until the desired pressure is reached.
- Carefully observe the readings on both the reference calibrator and the gauge under test.
Step 5: Compare and Adjust
- If the gauge reads correctly, proceed to the next test point.
- If there is a discrepancy, adjust the gauge as per the manufacturer’s guidelines.
- Some mechanical gauges have an adjustment screw, while digital gauges may require software-based calibration.
Step 6: Repeat at Multiple Pressure Points
- Perform calibration at different pressure levels (e.g., 0%, 25%, 50%, 75%, and 100% of the full scale) to ensure accuracy across the entire range.
- Note any deviations and confirm that the gauge maintains accuracy at all levels.
Step 7: Record Calibration Results
- Document the actual vs. expected readings at each test point.
- Include any adjustments made and the final calibrated values in the calibration report.
- If the gauge fails to meet accuracy standards, further adjustment or replacement may be necessary.
Step 8: Disconnect and Store Equipment
- Once calibration is complete, slowly release the pressure before disconnecting the gauge.
- Properly store the hand pump calibrator and any adapters to maintain their accuracy and longevity.
- Attach a calibration sticker to the gauge indicating the calibration date, technician’s name, and next due date.
Regular calibration of pressure gauges is vital for ensuring measurement precision and compliance with industry standards. By following these steps, you can maintain the accuracy of pressure gauges, improve process reliability, and avoid measurement errors in critical applications.
Factors to Consider for Pressure Gauge Calibration
Pressure calibration is done utilizing an accurate pressure system. The pressure measurement on calibrated pressure gauges is documented and compared with the uncalibrated gauge to identify the margin of error. However, many factors can affect the calibration process and should be considered: Accuracy class: The accuracy class is the maximum margin of error permissible for the pressure gauge for the maximum scale reading. During calibration, the accuracy class will help operators know the acceptable margin of error. Table 1 helps identify the permissible error margin based on the pressure gauge’s accuracy class.
Table 1: Permissible error margin based on the pressure gauge’s accuracy class
Accuracy class | Permissible error margin |
---|---|
0.1 | 0.1% |
0.25 | 0.25% |
0.6 | 0.6% |
1 | 1.0% |
1.6 | 1.6% |
2.5 | 2.5% |
4 | 4.0% |
Pressure media
When calibrating a pressure gauge, it is ideal to use the same media that is in the system that the pressure gauge attaches to. If this is not possible, for low-pressure gauges, calibration with air/gas is suitable while liquids are safer for high-pressure gauges. Contamination: Contamination like dirt, moisture, or grease can damage the pressure gauge as well as the calibration device. Thus, it is necessary to make sure the media and equipment are free of contamination and don’t disrupt the operation.
Height difference
During calibration, the difference in height between the pressure gauge calibration equipment and the pressure gauge can cause an error because of the hydrostatic pressure of the media. This is mostly observed in liquid media and not gas media.
The magnitude of the error differs depending on the density of the liquid as well as the difference in height. If it is not possible to put the calibration equipment and gauge at the same height, the effect of the height difference should be taken into account during calibration. A 2.5 cm (1 in) height difference accounts for an approximately 0.02 bar (0.3 psi) pressure reading inaccuracy. Electronic pressure calibration devices are typically used in dedicated pressure equipment calibration laboratories.
Leak testing
A leak test is crucial before calibration as any leakage in the pipe system can cause errors during calibration. The leak test can be done by pressurizing the system, letting the pressure gauge stabilize, and monitoring the pressure. Any drop in pressure can indicate leakage. It is necessary to ensure that the pressure loss is zero during calibration.
Adiabatic effect
The adiabatic effect can affect the accuracy of pressure gauge calibration when the pressure changes rapidly. As the pressure changes rapidly, the temperature of the fluid inside the gauge changes and this affects the density of the fluid, which in turn affects the pressure. This can cause errors in the gauge’s reading, which can lead to inaccurate calibration results. To minimize the effects of the adiabatic effect during calibration, it is recommended to use a pressure gauge with a high-frequency response. Such gauges have a faster response time and can accurately measure pressure changes that occur rapidly.
Mounting position
The mechanical nature of the pressure gauge means that the position of the gauge can affect the pressure reading in the system. Thus, it is recommended that the gauge be calibrated in the same position as it is used in the actual process for pressure measurement. The manufacturer’s guide should also be strongly referenced to ensure accurate mounting.
Pressurizing or exercising the gauge
Movement in mechanical pressure gauges causes friction. Exercising or pressurizing before calibration can reduce friction. Do this by supplying the nominal pressure, maintaining it for a minute, and then relieving it. Repeat this two or three times.
Readability
During calibration, adjust the input pressure so that the indicator needle always lands on a major scale mark instead of in between them. This makes the calibration process more convenient.
Hysteresis
Hysteresis in pressure gauge calibration refers to the difference in pressure readings when a gauge is subjected to increasing and decreasing pressure. In other words, it is the difference in the pressure reading when a gauge is calibrated while increasing the pressure, compared to the reading when it is calibrated while decreasing the pressure. This difference can be caused by various factors such as mechanical wear, temperature changes, and gauge design. It is important to take hysteresis into account when calibrating pressure gauges to ensure accurate measurements.
Repeatability
One of the qualities of an accurate pressure gauge is its repeatability, or the ability to produce the same reading for the same input. If the gauge is providing different results each time, it needs calibration. It is recommended to pressurize the gauge for 3 cycles before calibration.
Environmental condition
The reading in the gauge may vary depending on the different temperatures the process may be exposed to. The pressure gauge is usually calibrated at normal room temperature; hence, the temperature change can reflect on the accuracy of the pressure reading. Thus, it is recommended to record the temperature and humidity when calibration is performed.
Metrological traceability
Metrological traceability is important in pressure gauge calibration as it ensures that the pressure readings produced by the gauge are accurate and consistent with the international system of units (SI). To achieve metrological traceability in pressure gauge calibration, the gauge must be calibrated against a standard that is itself traceable to the SI. This is usually done by comparing the gauge to a known standard, such as a deadweight tester or a primary pressure standard.
Calibration uncertainty
The uncertainty in calibration can indicate the possible difference in the calibrated value. This uncertainty can be sourced by environmental conditions, reference devices, or operators taking the reading. It is important to be aware of the calibration uncertainty and be able to distinguish error from uncertainty. TUR (Test Uncertainty Ratio) or TAR (Test Accuracy Ratio) calculators are one of the ways to be aware of related uncertainty, although not all related uncertainties are covered. Therefore, it is recommended to calculate the total uncertainty of the calibration to identify how good the calibration is.
Calibration intervals
To ensure the accuracy of the reading, pressure gauges require regular calibration. However, the calibration needs may vary depending on the usage and design of the gauge. Although there is no fixed answer, a common recommendation is once a year. But it is also necessary to check for the manufacturer’s recommendation on the calibration period. Pressure gauges used in harsh operating conditions may require more frequent calibration.
Read Next: